
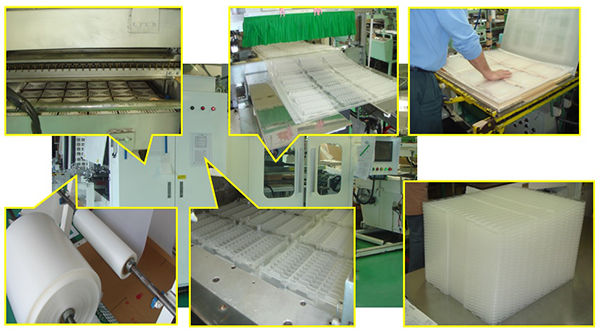
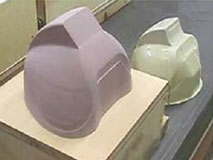
樹脂型
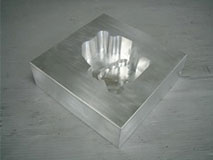
アルミ型
4. 材質の選択が容易です。
PVC・PS・A-PET・PP・ABS・KDG・PC・複合ラミネート材も使用できます。
電子部品トレー等には、表面抵抗値からみた素材選定も有効です。
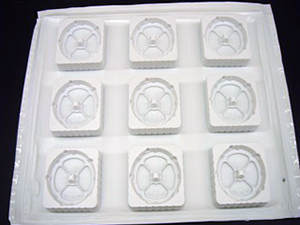
トリミング前
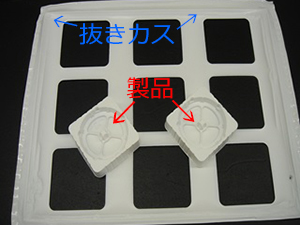
トリミング後
2. 肉厚にバラツキが出る。
キャビ型・コア型で成型する射出成型とは異なり、1つの凸型または凹型で成型するため、形状、設計により偏肉・薄肉になる部分が出てしまいます。
製品の要求仕様にあわせた金型設計により、弱点をカバーできる提案をいたします。
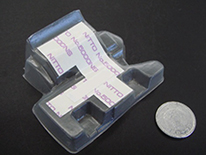
電子部品のカバー
水回り電化製品の機能部のカバーです。
機能部を結露等による水滴から守ります。
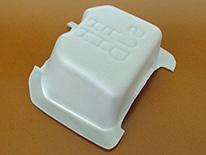
防塵カバー
機能部にホコリ等が入るのを防止します。
見えないところで真空成型品が活躍してます。
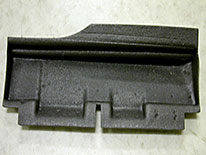
結露防止断熱材
ポリエチレン発泡シートを真空成型したものです。
カーエアコンドレンパン部分を断熱材でカバー。
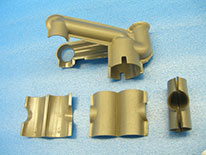
配管カバー
ポリエチレン発泡シート+粘着剤+ポリセパを真空成型で、形状を出します。
雪国での凍結防止、結露防止、等配管の断熱材として活用されています。
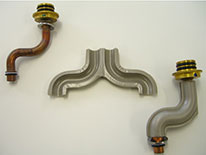
配管断熱材
セパレータも真空成型対応の素材を使っています。
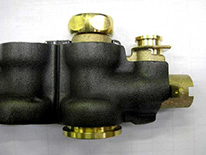
配管断熱材
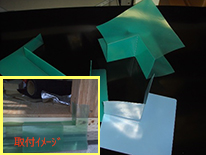
止水プレート
住宅関連の資材としても活用されています。
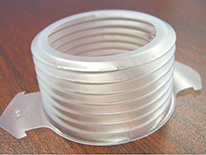
じゃばら部品
真空成型で作ったばね構造です。
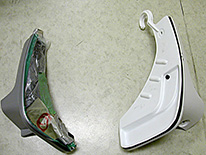
塗装時のマスキングカバー
部品と同じ形状のマスキングカバーなので、確実に部品を覆うことができます。
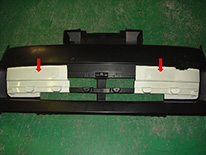
バンパー塗装マスキングカバー
必要な部分のみの形状を真空成型することにより、必要な部分のみ確実にマスキングします。
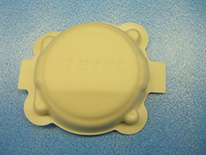
キズ防止カバー
外側はポリプロピレン(PP)内側はPP発泡シートを真空成型した傷防止カバーです。
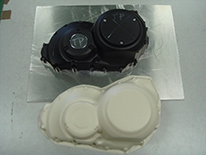
傷防止カバー
外側はポリプロピレン(PP)内側はPP発泡シートを真空成型した傷防止カバーです。
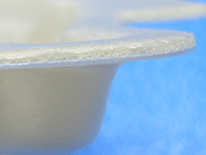
PP層とPP発泡層の複合シート真空成型品断面写真です。
2. ブリスターパック
ブリスターパックとは、プラスチックを成形して製造する透明色のパッケージです。プラモデルや子どものおもちゃ、日用雑貨の化粧品・歯ブラシ・カミソリ・接着剤(ボンド)など、あらゆる物を保護するために使用されています。
色が透明な理由は、購入者が商品を見て選べるように工夫されているからです。材料は丈夫なプラスチック(通常はPET:Polyethylene terephthalate-ポリエチレンテレフタレート)なので、水や汚れ、ほこりにも強く、特に中身が壊れやすい繊細な商品の場合は、鞄の中に入れて色んな場所に移動しても安心感があります。また、中身が見えると安心して購入できる利点もあります。
ブリスターパックは、中に入れる物によって自由自在に形を変えることができ、瓶詰めや箱詰めより製造コストは少ないとされています。真空成型を得意とするサトウパックでは、お客様からご要望があると、設計、金型製作、製造に至るまで自社で一貫生産しています。
ブリスターパックは、製品と台紙(製品の仕様等を明示する印刷物)とのパッケージ方法により大きく下記3タイプに分けられます。
① 曲げ加工タイプ
側面x2、底面に熱曲げ加工(3方曲げ)をしたブリスターパックに台紙をスライドさせてパックします。
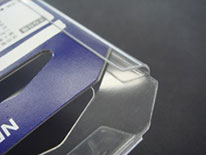
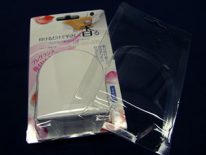
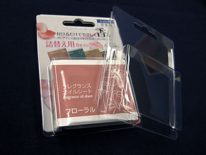
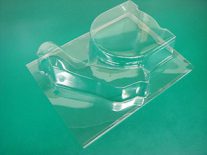
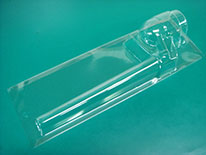
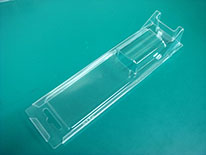
② シールタイプ
台紙とブリスターパックを熱圧着によってシーリングするタイプ。
ブリスターパックが製品プラスのりしろ程度の大きさで良いので、ブリスターパック単体では低コストで出来ますが、台紙に特殊糊加工が必要なので、台紙が少し割高になります。また、熱溶着機が必要で、溶着治具も必要ですので、初期投資が必要です。
パッケージで製品が密封される必要のあり、ロットの大きい商品に向いています。
③ シェルパック型
前面・背面ともにブリスターパックで構成し、製品を前後のブリスターパックで覆う形のブリスターパック。
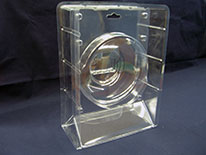
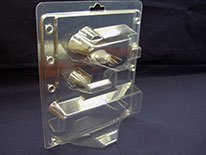
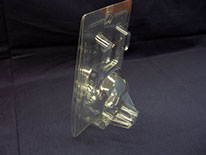
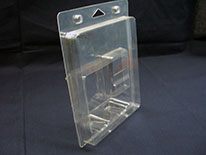
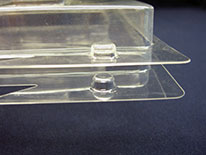
前面・背面のブリスターパックをボタンタイプの嵌め合いで固定することも可能です。
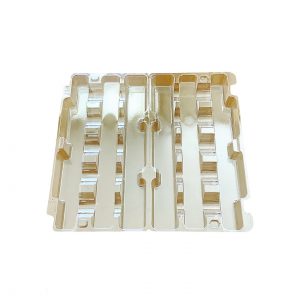
こちらのブリスターパックは中心線で折り曲げることができます。
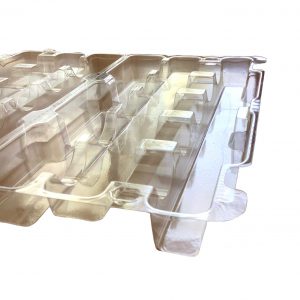
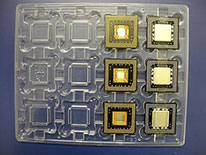
◆CPU用トレー
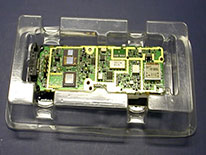
◆電子基板トレー
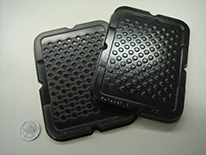
◆レンズトレー ふた・本体
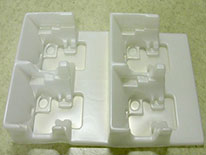
◆コンプレッサー用トレー
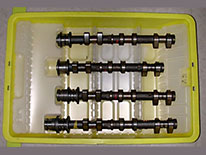
◆カムシャフト用トレー
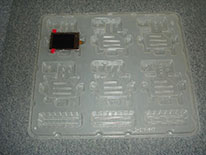
◆液晶パネルトレー
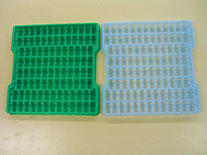
◆色違いマストレー
材料の色を変えることで、色違いのトレー別ができます。工程内での様々な識別に活躍します。
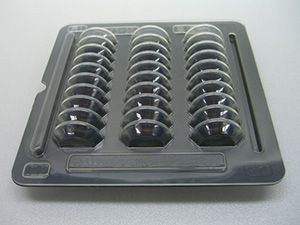
◆レンズトレー
静電気によるホコリ付着防止のために導電印刷のPET材、帯電防止印刷のPET材を使用しています。
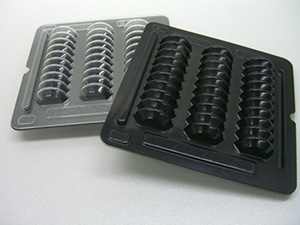
◆レンズトレー
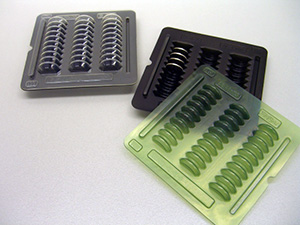
◆レンズトレー
工程内での品番色分けのために導電印刷のPET材色付緑色を採用いただきました。
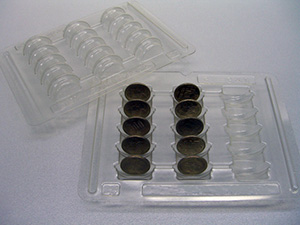
◆レンズトレー
※レンズのイメージでコイン(500円玉)を入れてます。
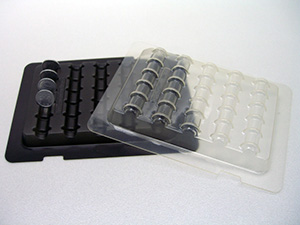
◆レンズトレー
※レンズのイメージでコイン(1円玉)を入れてます。
材料
真空成型では、様々な材料から要求仕様に合わせて材料選定することにより、トレーの機能を変えることができます。
材質そのものだけではなく、厚みを変えることでも違う仕様のトレーができます。
同じ型で違う材料の成形も可能です。その場合、材料収縮率の違いでできるトレーの寸法が変わってきます。
- 厚みのある材料→トレーの強度UP。重量物を入れるトレー、繰り返し使うトレーなど。
- 薄い材料→材料単価が抑えられ、コスト改善。軽量物を入れるトレー、1WAY使い捨てトレーなど。
- 色の変更→トレーの多色展開で、工程管理の効率アップ。類似部品をトレーの色で識別など。
※色付材料の場合、材料ロットが大きくなる場合もあります。
設計上の工夫で利便性UP!
工程内部品トレー、搬送用部品トレーなど、製品を入れて工程内の移動、保管、輸送などの使命を持ったトレーは設計上の工夫で2パターンで重ねることができるようになります。
例えば、トレーを使うときは部品を入れた状態でトレーを90度回転させて交互に重ね、トレー同士が重ならないように、すっぽりはまらないように、段積みできるように設計します。使わないときは重ねられてコンパクトに収納できるように設計します。部品トレーとして使う場所と保管場所で求められるそれぞれの機能を持たせることができます。
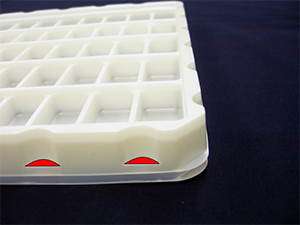
使わないときは、トレーを同じ向きで重ねます。たくさんのトレーもコンパクトに保管できます。
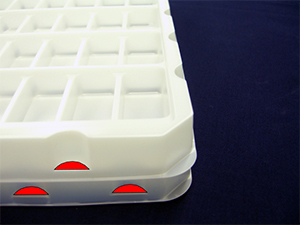
2段目のトレーは180度回転させて積みます。トレー外周に施した、リブ(写真赤部分)により、1段目に2段目が乗るかたちで、トレー収納部を確保して段積みできます。
部品トレーで工程改善!
- 段ボールや厚紙、プラ段等の組仕切り→プラスチックトレーやプラスチック仕切りにすることで、仕切りを組み立てる工程が省けます。
- 部品の形状に合わせた真空トレー仕切りで確実に部品を固定・保持できます。
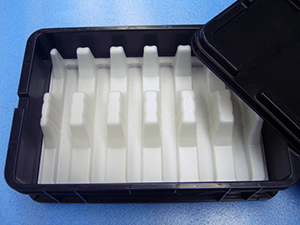
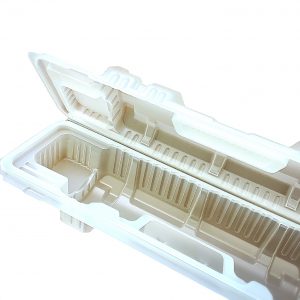
◆ふた付きトレー
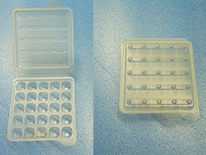
◆ふた付きトレー
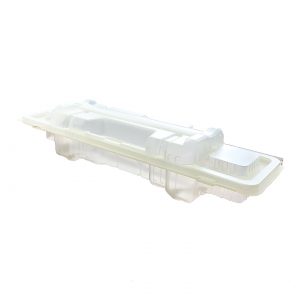
◆ふた付きトレー
閉じたところ
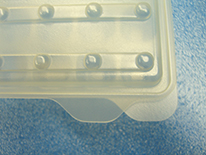
◆ふた付きトレー
開閉部は開けやすい形状にしています。

◆ふた付きトレー
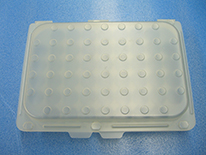
◆ふた付きトレー
閉じたところ
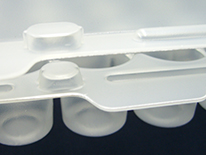
◆ふた付きトレー嵌合部
凸ボタンと凹ボタンの嵌合できっちりふたができます。
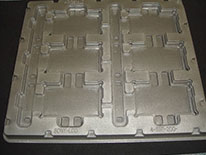
◆発泡PPシートの真空成型トレー
緩衝材機能、傷防止機能を持つトレー。
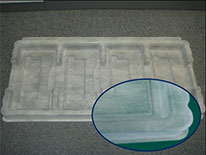
◆不織布+PETの複合材トレー
成形性がよい性質を持つPET樹脂に不織布層が加わることで傷防止効果を付加できます。
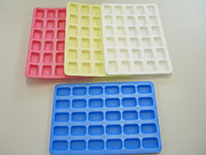
◆発泡ポリエチレントレー
精密部品の傷防止トレーです。
色でトレーを区別することで、工程内で行程毎、品番毎等の管理ができ、生産性の向上にも有効です。
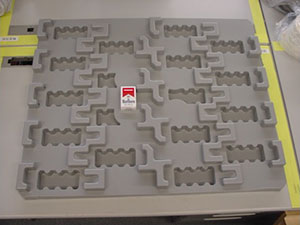
◆カイダック 3.0t
※タバコの大きさと比較して見てください。
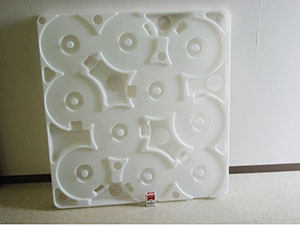
◆厚物トレーPPN3.0t
※タバコの大きさと比較して見てください。
自動化トレイの基本的な立上げの流れ
お客様との綿密な打ち合わせを重ね、要求仕様を満たす自動化トレーを作り上げます。
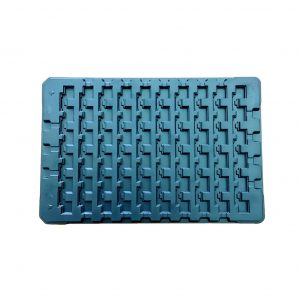
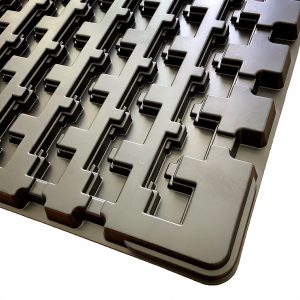
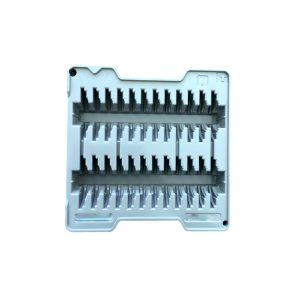
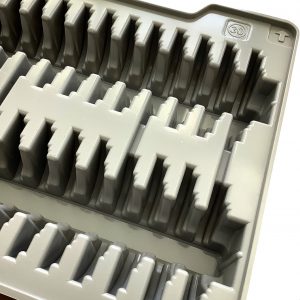
①自動化対応トレイ要求仕様の打合せ
・収納部品(ワーク)のトレイへの接触可部分と接触不可部分の確認
・自動機(ロボット)の動きを阻害しない設計 = トレイのどこでホールドしてどこでロボットがつかむのか
・帯電防止、導電性への要求レベル
・トレイの積み重ね、段積みへの要求確認
②図面作成
収納部品(ワーク)の3Dデータとトレイへの要求仕様を図面に落とし込みます。
③図面承認
完成した図面2Dデータ、3Dデータをお客様に確認いただき、図面の承認をいただきます。
④マス試作
コストと納期短縮を考慮し、トレイの1マスのみの試作を行い、形状と部品の収まり具合等を確認します。
試作型は樹脂型もしくはアルミ型で対応します。可能であれば、3Dプリンターによる樹脂型で対応できる場合もあります。
⑤量産型着手
試作サンプルで評価いただき、お客様の承認をいただき、量産型に着手します。
⑥量産品生産・納品
お客様に満足いただけるトレイが出来上がりましたら幸いです。
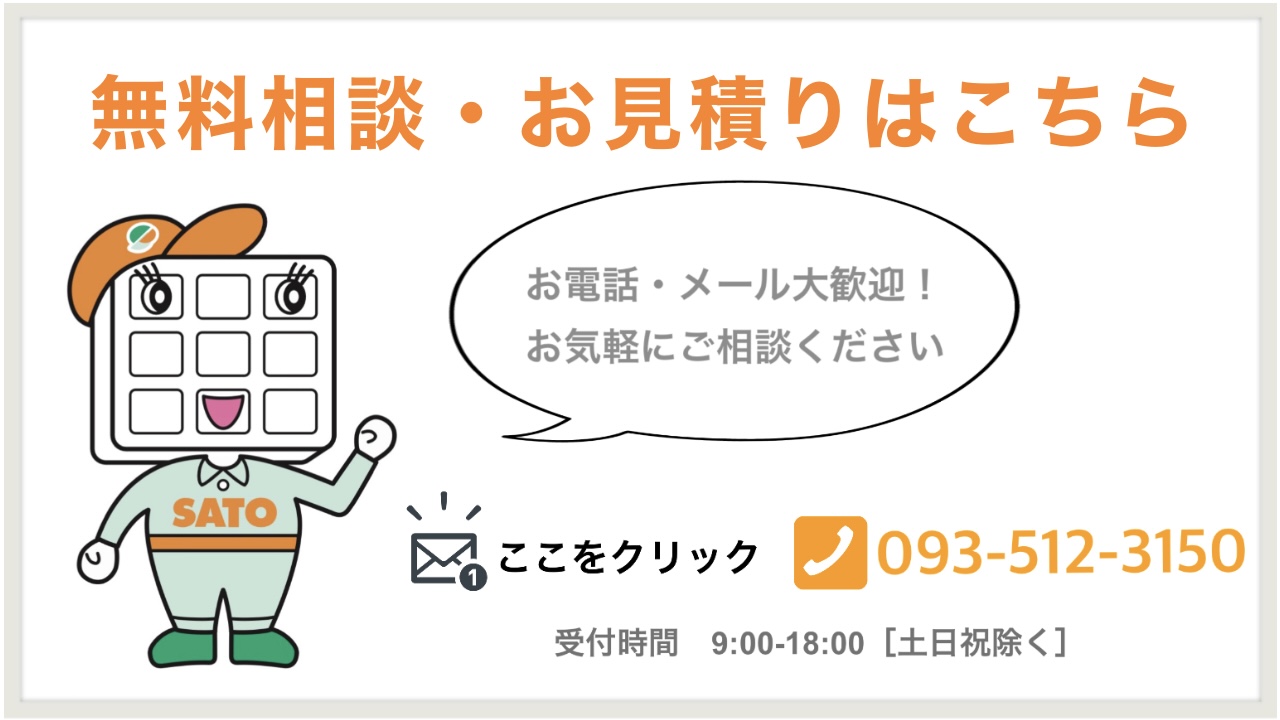